This article originally appeared in our Circularity Weekly newsletter. Subscribe to the newsletter here.
Let’s start this week with a short discussion on mobile, manufactured and modular homes. Exciting, amiright? All three of these home types have a bad rap based on the (generally) poorly constructed factory-built homes of the mid-to-late 20th century. Let’s start with definitions (because I really didn’t know the difference between these three).
A modular home, or prefab home, is built off-site in a factory and then final assembly and connection to utilities (if required) is accomplished on the building site. These structures are permanently attached to foundations and once installed, they are pretty much like any other site-built home in form and function and generally are built to meet or exceed all local building codes.
This is where it gets a bit complicated. While modular homes are technically quite similar to manufactured homes (and mobile homes), there are differences. First, manufactured homes are generally limited to certain zoning areas and are built to a different set of codes from traditional and modular homes. There is also the legal definition of what kind of property each type of home is. I won’t get into all that here, but for a more detailed description, head over to this handy Bankrate description. Also, you’d be surprised, the internet holds a surprising level of rabbit hole-iness on this subject.
Despite their previously tarnished reputation, though, modular homes are making a comeback in the 21st century. I’d like to argue this is the confluence of several issues.
One… The world is short on housing. In the U.S. alone, experts put the housing shortage at anywhere between 1.5 million and 4 million units. Our friendly neighbors to the North need their own housing stock to climb by an estimated 3.5 million units by 2030 to house every Canadian affordably. Modular homes offer another pathway to filling the housing gap in addition to the current practices still dominant here in North America. Another way of putting it, we need a both/and set of solutions to fill the housing gap.
Two… Labor shortages are hitting the construction industry exceptionally hard. There are 300,000 to 400,000 open construction positions in the U.S. on a monthly basis and the Home Builders Institute estimates the industry will need to add 740,000 new construction workers each year for the next three years in order to keep up with demand and makeup for attrition and retirements. That staggering number, combined with historically low unemployment rates across the U.S., combines to produce a tricky problem. How do you recruit an increasingly educated public to work jobs that require hard physical labor and long hours?
Part of the answer may lie in modular homes. Standardization of parts, controlled climate environments for building and modern technology advances (such as robotics and automated sequencing of parts) mean that modular homes today can be built with shorter lead times by fewer people. Seems like a win-win for both the issues laid out above.
Three… energy efficiency and electrification. Today’s modular homes are not the leaky, cheaply built homes of the past. More on this point when we talk about a case study below, so keep reading. They are often also the high-tech homes of the future we’ve all been waiting for.
Four… the move toward a more circular economy. As I’ve written previously, the construction industry is extremely wasteful. While we are making strides in certain areas to decrease that waste, factory-built panels and full rooms/homes offer a great opportunity for waste reduction. Imagine being able to apply all the same part sequencing, cut optimization for framing materials and zero waste manufacturing methods that are currently done in other parts of the manufacturing sector to buildings. A modular building platform also offers standardization of a kit of parts while allowing for customization through options (finishes). For example, if the modular builder has six models they offer, those can all be built on the same part platform to standardize and avoid unnecessary cuts and waste.
One more really interesting (at least to this observer) point about modular homes is that they offer an enormous opportunity for the building to carry data. The data can go by many names and in many forms, but I’m referring to a material passport, a digital twin or some similar format that allows a future user to know exactly what’s in their building, and how to reuse, re-manufacture or recycle it. These inventories of parts and materials can also allow for chemical transparency, a key to unlocking the future circular economy.
A real-life example: Dvele
If you’ve made it this far, you deserve to know at least one company working in this new era of modular homes. Dvele opened its prefabricated home factory in 2018 to take on the homebuilding industry that has stayed relatively static for over 100 years. The three co-founders set out to “disrupt the home-building industry to create the smartest, healthiest, most sustainable homes on the market.” They came from backgrounds in modular and traditional home building, so they had a deep understanding of the issues in the space and what they could improve on.
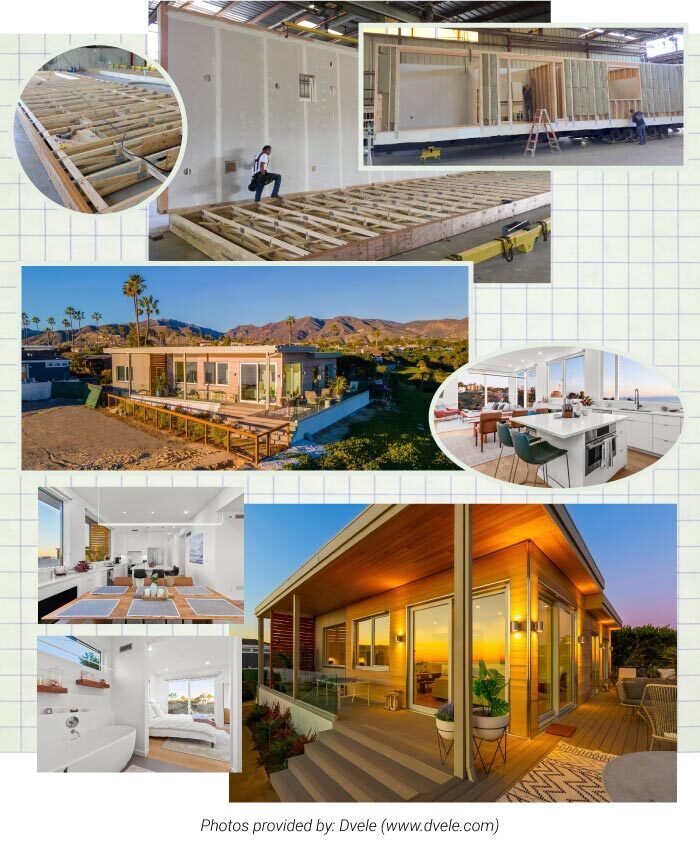
Since its founding, Dvele has added automation to its production lines, implemented processes to maximize efficiency and output and incorporated biophilic design. In addition, all the homes the company sells are self-powered out of the box, are all-electric and are built to be 100-plus year structures. The homes are built on standard modular platforms and finishes can be customized on their website through the “choose your home” platform. I went through the process myself and found it quite delightful. My favorite is the Baldwin Mini-home (430 square feet). In only seven steps, I was able to customize the exterior and interior of the home to my liking and put in a request for timeline and cost to the Dvele team. As I said, delightful! It was even easier than customizing a new car’s features.
While the innovations here don’t represent a full turn to circularity for residential structures, the innovations currently taking place in the modular home building space are poised to bring us closer. If we are to make housing more available, more affordable and more circular, we’ll need to simultaneously root for companies such as Dvele and others to scale and succeed while also pushing them to continue to improve.
Also, if you’re interested in seeing some pictures of other magnificent modular homes, check out Gessato’s list here. I’m a sucker for cool architecture.
If you’d like to read the original source of this article please click here Visit Source