As new, high tech solutions to the climate crisis draw media attention like flies, the role of the ever-present innovations of the past are easily forgotten. When it comes to concrete, literally a monotonous pile of glop, perhaps we’re not to blame. When we look at the numbers, we’re reminded how prevalent and imperative it is for concrete to be decarbonized. Cement is the second most consumed product in the world — only beaten out by potable water — and makes up 7 percent of total carbon emissions, nearly four times the amount of aviation. But you only get the full picture looking at the rate of growth. By 2060, the number of buildings in the world is expected to double. In order to reach nearly any global climate goals, we must make sure those are not built the way we have in the past. Ordinary Portland Cement, the most commonly used method and variety in creating cement, hasn’t changed in more than a century. So what’s the alternatives and how do we get it scaled and deployed as soon as possible?
The importance and challenge of concrete
When framing the climates’ grandest challenges for the built world, there are three omnipresent materials; steel; cement; and plastic. Cement poses the greatest challenge because it releases carbon in every part of the process. To get concrete you mix gravel, sand and water. Then cement is added to bind the small rocks, and while it only usually makes up around 12 percent by volume, it makes up most of the emissions.
To create the cement you need calcium and for that you need limestone which contains calcium, carbon and oxygen. Bet you see where this is going. Once you burn the limestone and retrieve your precious calcium, you’re stuck with CO2. The most challenging emissions to cut out takes place during that chemical reaction process and decarbonizing this process is where the majority investment is funneled. But decarbonizing the energy needed to create the enormous amount of heat to break down the limestone, known as process heat, poses its own challenge. Here we can get a clearer picture for where the opportunities are to bring emissions down.
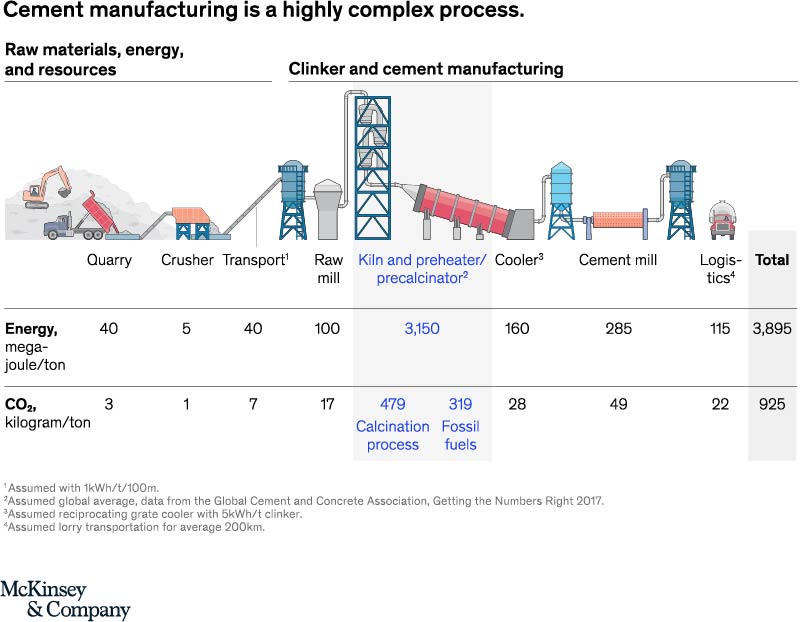
Next generation pozzolans
Additives, also known as pozzolans, are added to cement to reinforce its sturdiness and make it cheaper for developers. Industrial waste from coal, steel and iron — also known as Fly Ash and Slag — are standard replacements in the industry, displacing up to 10 percent of the concrete needed to make cement. But many of these pozzolans are bi-products of carbon intensive energy sources that will eventually be decarbonized and phased out, making them increasingly hard to source. For example, fly ash comes from burnt coal but in New York state the last coal plant was shut down so now it’s virtually impossible to get these pozzolans at a price that makes sense.
There’s an array of startups looking at different pozzolans. Companies inject C02 captured from a range of industrial production processes back into the concrete while it settles, allowing for less water usage and increased strength. To date, companies “carbon curing” the concrete have garnered most of the attention, with Carbon X’s two winners, CarbonCure and CarbonBuilt, both beginning to reach scale.
The methods these startups are pursuing mainly rely on integrating post-combustion carbon capture and it’s important to remember that while the technology has the potential to get closer to 90 percent efficiency, most carbon capture scrubbing technology only captures somewhere between 40-60 percent of emissions emitted during the process.
Currently pozzolans are the most cost competitive option. Even if some pozzolans come from dirty sources, they provide huge value in reducing emissions while other cleaner options come online. While we wait on national policies and regulation delays around the use of new materials, new certifications and building standards will also increase pressure on construction companies and the demand in the market for these alternatives will only grow.
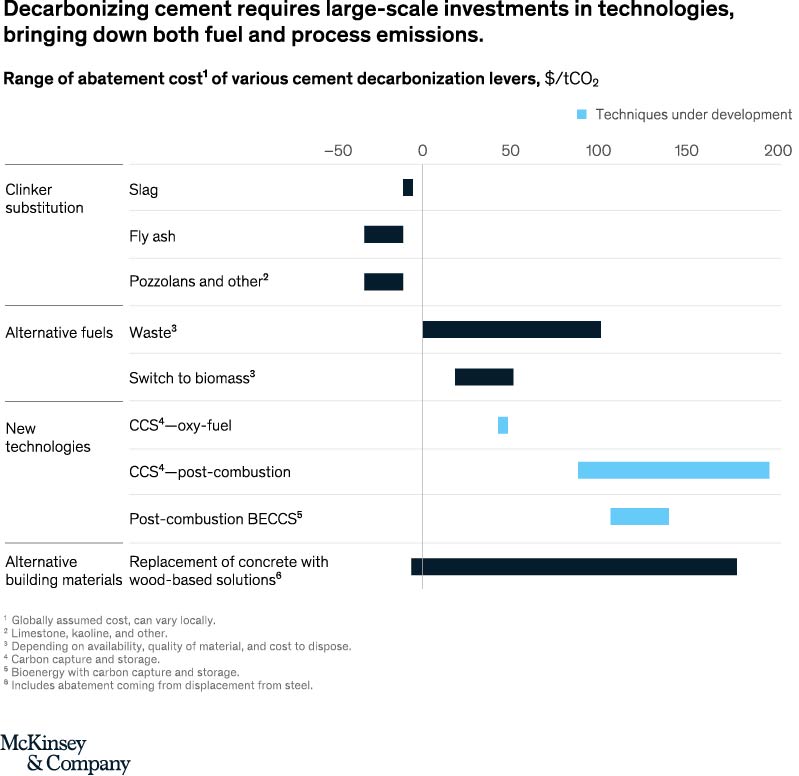
Adding circularity to pozzolans
Direct air capture has always grabbed the most attention but many low tech innovations for sidewalks or driveways go unnoticed despite having multilateral benefits. For example, KLAW Industries collects post-consumer glass with high levels of contamination that would have otherwise gone to landfill, then refines it into a high-quality cement replacement.
KLAW addresses the need for a much easier to use and cost-effective option for decarbonizing for small to mid-sized concrete plants.
“The simplicity is that they don’t even know they’re using it,” said Jacob Kumpon, CEO of KLAW. “All they need to know is they are saving money and making sturdier concrete,” which means a lot in an industry that’s much slower to change.
“Often more venture backed startups focus on the biggest projects or the highest skyscrapers and lose track of the end goal,” he said. “These are great solutions but with any great tech you hit roadblocks, but while they scale, who’s solving the rest of the problem?”
More companies are embracing circular principles and finding value in waste streams. Terra C02 taps on waste from granite quarries and alluvial sand/gravel pits to create a mixture that doesn’t need limestone, cutting the products emissions by more than half.
To get to zero, we’ll need cost effective solutions to our most mundane and common applications for concrete.
With 3 trillion liters of water used for concrete production every year, producers have also begun to reuse water across the heating and cooling process in order to reduce water consumption. Such solutions not only allow concrete producers to save money and lower their direct carbon emissions but create dependency on waste streams, spurring demand for more investment towards recycling systems and a more circular economy.
To get to zero, we’ll need cost effective solutions to our most mundane and common applications for concrete. This isn’t just true in the U.S. but globally, in 2013 emerging economies consumed 90 percent of concrete produced, showing the desperate need for scalable solutions that can operate in a variety of environments.
Decarbonizing generation
The next biggest chunk of emissions is in replacing and reducing “process heat,” the incredibly high temperatures it takes to drive the chemical process. Companies such as Carbon Re and Alcemy create software to analyze temperature of usage in order to optimize just what’s needed, reducing the margin for error and thus waste. They give operators feedback to optimize fuel usage and thereby cut costs and energy resulting in less carbon emissions. With process heat still making up 30 percent of the emissions for concrete, this is a fast, easily applicable and scalable approach to decarbonization.
Then comes electrifying the sources themselves, which according to the energy information administration’s research is proving more challenging than anticipated. Electrifying the process is dependent on the surrounding renewable energy offerings of the grid, and its capabilities to provide such high levels of heat and energy.
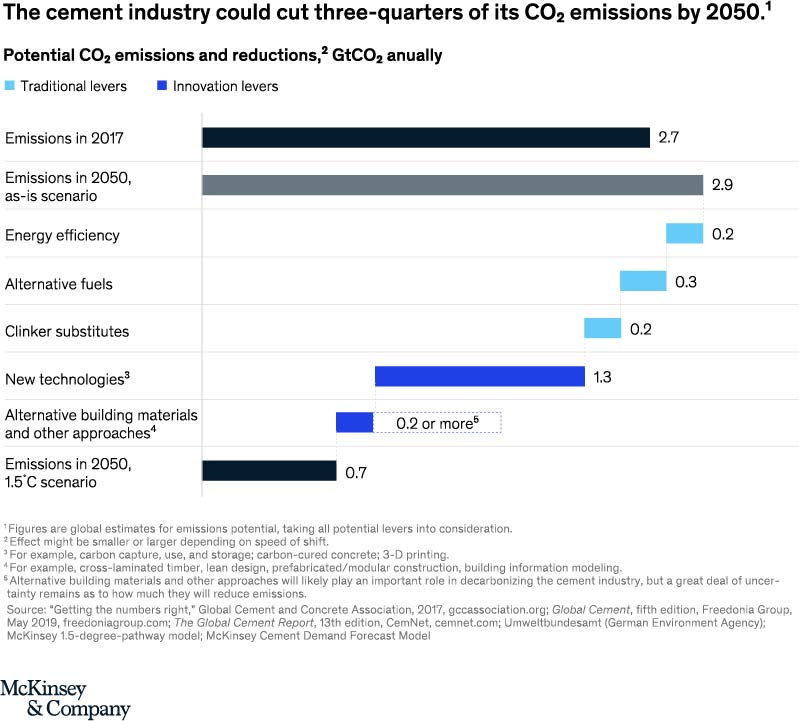
Support from policy
When looking at policy levers for decarbonizing concrete, the right portfolio would include economic signals such as low-carbon cement standards to create an emissions intensity benchmark, complimented by a long-term research and development strategy to nurture technologies that unlock deeper emissions reductions. Running these adjacently and over a long-term period allows for concrete producers to have the security that their low-carbon investment will prove profitable through either their projects qualifying as carbon credits, incentives for consumers or competitive advantage.
Other applications and processes could open exciting new roles for concrete, including different prefab designs and modular housing. But as our remaining carbon budget dwindles and we continue to emit C02, we need multifaceted solutions covering every square foot.
If you’d like to read the original source of this article please click here Visit Source